Air Compressor for Shop: A Comprehensive Guide
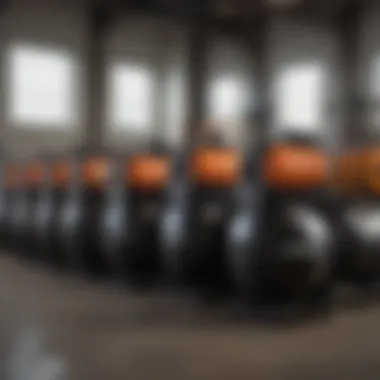
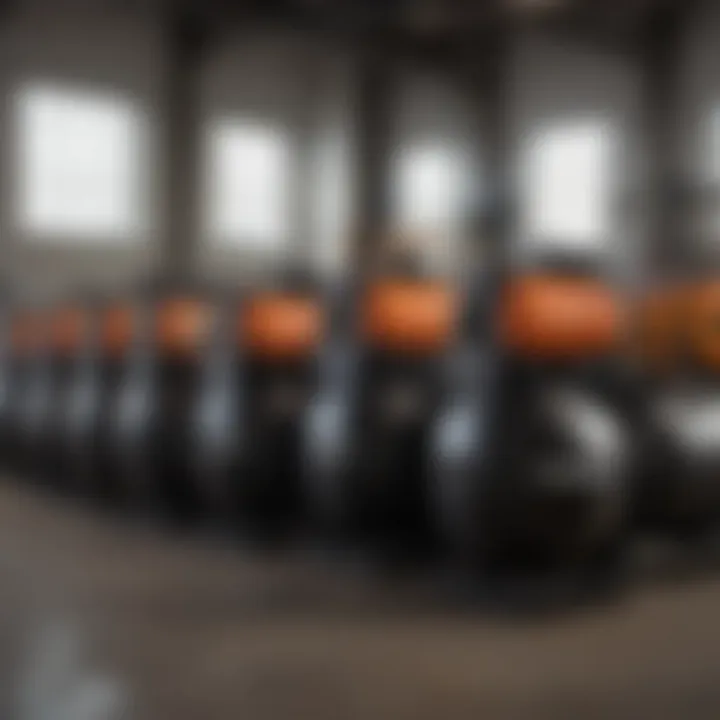
Intro
An air compressor is a vital tool in various shop environments, playing a crucial role in powering tools and equipment. For professionals and hobbyists alike, understanding the capabilities and nuances of air compressors can greatly enhance productivity and efficiency. This guide aims to dissect the intricate components of selecting and maintaining these machines. It seeks to provide relevant information about types, applications, and performance factors that are critical for achieving optimal function in diverse shop settings.
By delving into installation tips, safety measures, and troubleshooting advice, we aim to broaden your comprehension of how air compressors operate. Whether you are an industry specialist or a curious enthusiast, this guide offers an invaluable resource for mastering the use of air compressors in your workspace.
Understanding Air Compressors
Understanding air compressors is crucial for efficient shop operations. This section delves into the definition and various types of compressors. Knowing these aspects will not only aid in selecting the right compressor but also in utilizing it effectively within a shop environment. Air compressors serve as the backbone for numerous tools and machinery. Hence, a comprehensive grasp of their functionality ensures optimal performance and longevity.
Definition and Functionality
An air compressor converts power, usually from an electric motor or engine, into potential energy stored as pressurized air. The basic functionality is straightforward: it draws in air, compresses it, and then stores it in a tank. This stored compressed air can then power various tools or machinery. The efficiency of this process may vary based on the type of compressor and its application. In shops, air compressors are widely used to power pneumatic tools, spray equipment, and even clean surfaces. Understanding this fundamental operation allows users to assess their specific requirements and make informed choices.
Types of Air Compressors
There are several types of air compressors available, each with unique characteristics, advantages, and disadvantages. The most common types are reciprocating, screw, centrifugal, and scroll compressors. Selecting the right type depends largely on the intended usage in a shop setting.
Reciprocating Compressors
Reciprocating compressors work using pistons driven by a crankshaft. This type is typically favored for its simplicity and cost-effectiveness. Its key characteristic is the high-pressure output it can provide, making it suitable for tasks requiring substantial pressure, such as powering nail guns or impact wrenches.
One notable advantage of reciprocating compressors is their versatility; they can be configured for both small and large operations. However, the moving parts can lead to higher maintenance requirements and potential for noise, which can be a consideration in quieter work environments.
Screw Compressors
Screw compressors utilize two helical rotors to compress air. Their primary advantage is continuous operation, which is ideal for industrial applications. This type provides a steady air supply without the pulsation present in reciprocating models.
Screw compressors are beneficial for their reliability and efficiency, especially in settings where high volume and constant pressure are needed. However, they are generally more expensive both to purchase and maintain. They also require a more complex setup, which could be a drawback for smaller shops.
Centrifugal Compressors
Centrifugal compressors operate on a different principle, using a rotating disk to accelerate air and convert kinetic energy into pressure. This method allows for high airflow rates, making them suitable for larger industrial needs.
The main advantage of centrifugal compressors is efficiency; they can effectively operate at high volumes with minimal maintenance. However, their reliance on continuous operation makes them less ideal for smaller applications where variable demands exist.
Scroll Compressors
Scroll compressors utilize two spiral-shaped scrolls to compress air. This type is known for its quiet operation and compact design, which can fit easily in limited spaces. Furthermore, scroll compressors are known for their energy efficiency.
A unique feature is that they have fewer moving parts than reciprocating types, leading to a lower likelihood of wear and tear. However, they may not deliver the same high pressures as other types, which can limit their use in heavy-demand scenarios.
Understanding these types provides essential insight into selecting the right compressor for a shop. A well-chosen air compressor enhances productivity, ensures safety, and maximizes the potential of tools and machinery.
Choosing the Right Air Compressor for Your Shop
Choosing the right air compressor for your shop is vital. It involves understanding your operational needs, budget, and the right brand. Selecting a suitable air compressor enhances productivity and ensures that tools function effectively. Proper choice reduces downtime and increases efficiency. Hence, knowing what to prioritize can lead to healthier workflows.
Assessing Your Needs
Required PSI and CFM
When deciding on an air compressor, it's crucial to understand required PSI and CFM.
PSI refers to pounds per square inch. It indicates the amount of pressure generated by the compressor. CFM stands for cubic feet per minute. This measures air flow volume. Knowing these two values helps in matching the compressor to the tools you will use, ensuring they operate correctly. Without the right PSI and CFM, tools may underperform or malfunction.
A beneficial characteristic of correctly matching required PSI and CFM is improved efficiency. Appropriate pressure and flow lead to smoother operation. Conversely, having insufficient PSI may lead to tools getting stuck or not working at all, causing frustration and delays.
Types of Tools and Equipment
Understanding the types of tools and equipment is also key. Different tools require different air requirements to run effectively. Handheld tools like nail guns need lower PSI compared to heavy machinery.
Tools with varying specifications can impose unique demands on the chosen compressor. Selecting a compressor that meets those needs is essential. If the air compressor cannot support the tools used, then efficiency decreases and the work becomes tedious. It's important to examine the tools whenever you are making a choice on the compressor.
Budget Considerations
Budget considerations play a significant role in selecting the right air compressor. The cost involves more than the initial purchase price.
Initial Purchase Cost
The initial purchase cost is often the first concern for buyers. They must consider what they are willing to spend for the specific compressor required for their shop. This initial cost varies widely, depending on size, capacity, and brand.
A key aspect to keep in mind about the initial cost is long-term investment. Cheaper models might be appealing upfront. However, they may lack durability and power efficiency, leading to higher costs over time. Buying a high-quality compressor could save money in the long run due to fewer repairs and replacements.
Operating Costs
Operating costs are a crucial factor to understand. These costs include electricity bills, maintenance, and parts replacement. Keeping an eye on these is vital for proper budgeting.
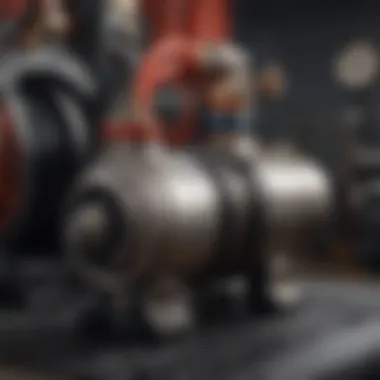
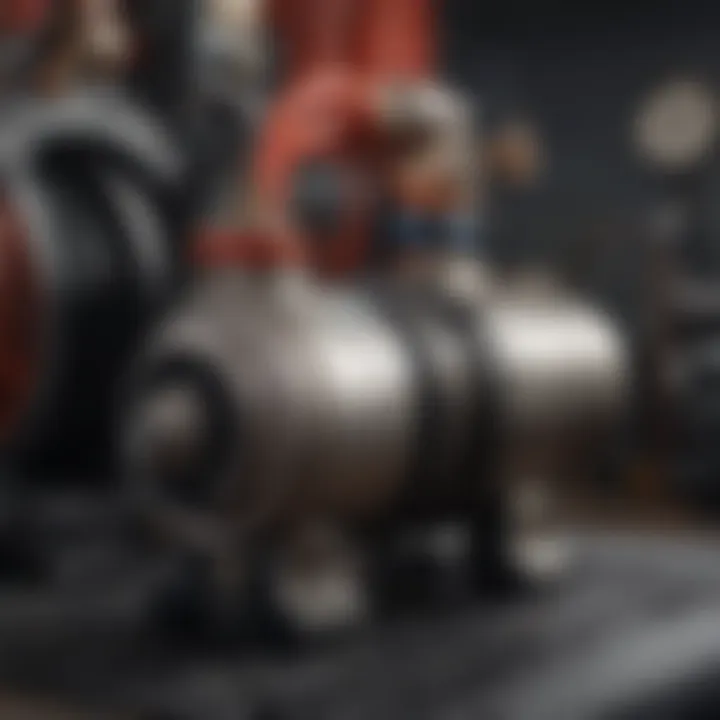
Low operating costs allow for increased profitability in running a shop. Efficient compressors consume less energy. Thus, selecting a compressor with lower operating costs or energy-efficient features is more economically practical. Failure to consider these aspects can easily lead to financial strain.
Brand and Model Comparisons
Making a good decision on air compressor brands is necessary. Reputation and reviews can provide meaningful insights into performance and reliability.
Reputation and Reviews
The reputation of brands gives an indication of quality. Brands with a good standing have typically delivered reliable products. Reading customer reviews can give necessary feedback. This information shows how well the compressors perform in real-world settings, which is invaluable.
Positive feedback and high ratings generally suggest a proven product. Meanwhile, negative reviews can highlight potential issues before a purchase is made, ultimately guiding better purchasing decisions.
Warranties and Support
Warranties and customer support are important when selecting a compressor. A solid warranty indicates a manufacturerβs confidence in their product. Comprehensive support can assist in resolving unexpected issues post-purchase.
An extended warranty can save costs for repairs and provide peace of mind. Buying from brands that are known for good customer support is wise. It ensures help is available when needed and adds value to the overall purchase.
By ensuring you assess your needs accurately and consider budget implications wisely, you can choose an air compressor that best fits your shopβs demands, leading to enhanced performance and productivity.
Installation of Air Compressors
The installation of air compressors is a critical step that significantly influences their operational efficiency and safety in a shop environment. Proper installation not only ensures optimal functioning but also minimizes risks associated with machinery. This section focuses on essential aspects like site selection and connection setup, both crucial for getting the best performance from your air compressor.
Site Selection
Space Requirements
Space requirements are fundamental in site selection for installing an air compressor. A compressor needs ample space around it for maintenance and ventilation. A key characteristic of space requirements is that it impacts airflow and heat dissipation. If the unit is cramped, it may overheat and underperform. A beneficial choice in a shop environment is a dedicated area that can accommodate the compressor's size and any peripheral equipment.
Having designated area for the compressor helps in avoiding accidents and enhances maintenance accessibility. This unique feature allows users to conduct regular checks with ease. However, an overly spacious installation can lead to inefficient air distribution, making it imperative to strike a balance.
Ventilation Needs
Ventilation needs are another important factor in the site selection process. Adequate ventilation prevents overheating during operation. The key characteristic of proper ventilation is air circulation, which is necessary for cooling. It is a beneficial practice to have an area where fresh air can circulate freely around the compressor.
One unique feature of ventilation needs is the requirement for exhaust outlets or vents. These are crucial since they ensure heat does not accumulate around the unit. However, improper ventilation can lead to increased energy costs and could potentially lead to mechanical failures. Hence, planning for ventilation needs is essential in this article to ensure longevity and reliability of the air compressor.
Connection Setup
Power Supply Considerations
Power supply considerations are vital for the successful operation of an air compressor. Ensuring that the correct power source is available is a key step in preventing future issues. The important characteristic here is understanding the electrical requirements of the specific compressor. A beneficial choice would be to verify voltage and amperage needs before installation. This can prevent potential electrical failures.
One unique feature to consider is the need for circuit breakers or fuses specifically rated for the air compressor's load. Having the correct circuit protection can save the equipment from power surges. While not adhering to power supply specifications can lead to inefficiency and increased costs, ensuring a proper setup results in better field performance.
Air Line Installation
Air line installation is critical for distributing compressed air to various tools and equipment. The specific aspect of air line installation is routing the lines effectively to minimize pressure drops. The key characteristic in this case is using high-quality materials that can withstand the pressure and wear over time.
Making a beneficial choice in selecting the correct diameter of air hoses will ensure efficient air flow. Unique features like the inclusion of quick-connect fittings can improve flexibility and reduce downtime during tool changes. Nevertheless, improper installation can lead to leaks. Addressing this in this article is vital because leaks compromise performance and waste energy, presenting a clear reason for meticulous planning during installation.
Proper installation of air compressors is not just about placement; itβs equally about ensuring all components work harmoniously for peak performance.
This section has highlighted the critical elements associated with installing air compressors. Attention to detail in site selection, power supply planning, and air line installation plays a significant role in the operational success of compressors in a shop environment. The following sections will address further operational guidelines to maintain efficiency.
Operational Guidelines for Air Compressors
Understanding how to operate air compressors effectively is essential for achieving the desired performance and extending the lifespan of the equipment. Proper operational guidelines ensure safety, maintain efficiency, and prevent costly breakdowns. For shop environments, these guidelines become even more critical as they directly affect productivity and the overall output of the workshop.
Starting and Stopping Procedures
Starting and stopping an air compressor is straightforward yet crucial. Before powering up, ensure that all connections are secure, and the unit is clear of obstructions. Refer to the manufacturer's manual for specific start-up instructions. Generally, you will begin by checking the oil level and ensuring that the safety valve functions correctly.
Once everything is in place, turn on the power. Pay attention to indicators that show the compressor is reaching the correct pressure setting. When it is time to stop, ensure you use the proper shutdown process. This includes letting the air pressure drop to a safe level before switching off the compressor. Following these procedures prevents damage and enhances safety throughout the operation.
Usage Best Practices
Efficient use of an air compressor hinges on several best practices. Knowing how to manage pressure levels and adhering to regular maintenance tasks significantly impacts the overall efficiency and prolongs the life of the equipment.
Monitoring Pressure Levels
Monitoring pressure levels is crucial for several reasons. First, incorrect pressure can lead to inefficient operation and even equipment damage. Understanding the required pressure for your specific tools can help in maintaining optimal performance. Regularly check the pressure gauge to ensure the air compressor runs within the recommended PSI.
Moreover, keeping a consistent pressure facilitates the excellent performance of pneumatic tools. If the pressure is too low, tools may underperform, while excessively high pressure can lead to equipment failure. Thus, by monitoring these levels diligently, you prevent unnecessary downtimes and guarantee the tasks are done efficiently.
Regular Maintenance Tasks
In the realm of air compressors, regular maintenance is non-negotiable. It ensures that the device remains in good working condition while avoiding potential breakdowns. Common maintenance tasks include checking oil levels and changing filters regularly. Oil changes help reduce friction and wear, leading to a longer lifespan of the compressor.
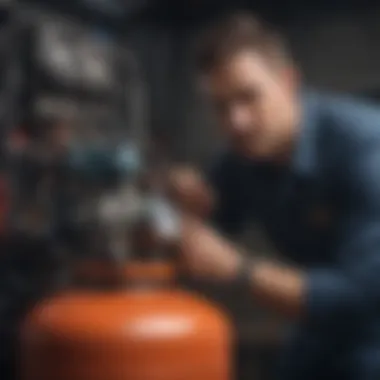
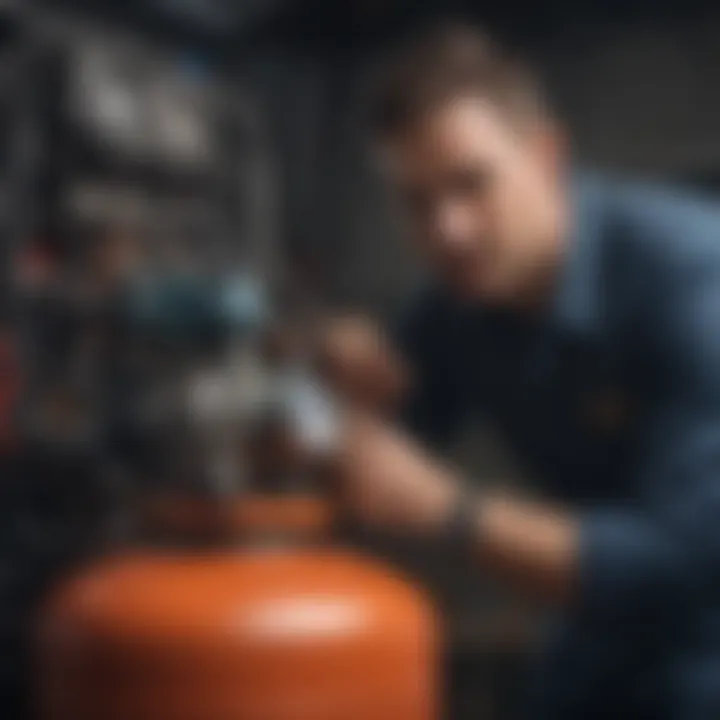
Air filter replacement is another vital maintenance aspect. A clean filter ensures that the compressor takes in clean air, which is essential for efficient operation. Neglecting these maintenance duties can lead to decreased performance and costly repairs. Therefore, integrating these regular tasks into your routine ensures that your air compressor remains reliable and efficient in your shop.
Maintenance and Troubleshooting
Maintaining an air compressor is pivotal for ensuring operational efficiency and longevity. Proper maintenance and troubleshooting can lead to the prevention of significant issues, enabling your air compressor to perform optimally. When the components are well cared for, the risk of unexpected breakdowns diminishes. This section will delve into the essential routine checks and the common problems that may arise, along with their solutions.
Routine Maintenance Checks
Routine maintenance keeps an air compressor in good working condition. Following a structured maintenance schedule safeguards against potential failures and enhances performance.
Oil Changes
Regular oil changes are crucial for the health of the compressor. They help in lubricating the internal components, reducing friction, and preventing wear. Keeping the oil clean ensures that the compressor operates at optimal temperatures. The key characteristic of oil changes is their ability to extend the lifespan of the machine. This makes them a popular choice for routine maintenance in this article.
Oil changes can be relatively straightforward, often requiring only a few tools and some time. Neglecting this step may lead to overheating and decreased performance, which you don't want to encounter.
Air Filter Replacement
Air filter replacement is another essential aspect of routine maintenance. A clean air filter allows for proper airflow and prevents contaminants from entering the compressor system. This contributes significantly to overall air quality and compressor efficiency. The key characteristic of air filter replacement is its impact on the compressor's performance, making it a beneficial maintenance task.
Replacing the air filter is usually an uncomplicated process, requiring minimal tools. However, if neglected, a dirty filter can hinder airflow, leading to decreased efficiency and higher energy consumption.
Common Issues and Solutions
Addressing common issues promptly can prevent further complications and enhance the reliability of your air compressor.
Decreased Performance
Decreased performance is a typical issue often linked to inadequate maintenance. It may manifest as reduced pressure or insufficient airflow. Regular maintenance tasks like oil changes and air filter replacements can mitigate this. The key characteristic of decreased performance is that it directly impacts productivity, emphasizing the need for timely interventions.
To diagnose decreased performance, you might check for leaks in the air lines or verify that the tool requirements match the compressor capabilities. Ignoring these can lead to even more severe operational problems.
Unusual Noises
Unusual noises can signal underlying issues with the air compressor. A sudden increase in noise levels often indicates mechanical problems, such as loose parts or bearings needing lubrication. The key characteristic of unusual noises is their potential to indicate serious damage. If you hear abnormal sounds, it is wise to shut down the machine and investigate.
By addressing noise issues early, you might save yourself from costly repairs later. Regular checks can help you identify emerging problems before they escalate.
"Routine maintenance checks not only prolong the life of your air compressor but also ensure its consistent performance."
In summary, understanding maintenance techniques and solving common problems can significantly enhance your experience with air compressors in a shop setting. Regular attention and prompt action help ensure that your equipment serves you well for many years.
Safety Considerations
Safety is paramount when operating air compressors in a shop setting. Understanding the potential risks can protect both the equipment and its users. This section discusses the various safety aspects involved and emphasizes the importance of implementing appropriate measures to prevent accidents and injuries.
Understanding Risks
Pressure Accidents
Pressure accidents can occur if the compressor is not used correctly. Typically, these accidents involve air pressure exceeding the limits of the compressor or associated tools. The sudden release of compressed air may lead to physical harm or equipment damage. The key characteristic of pressure accidents is the unpredictable nature of pressurized systems. Employing the right techniques minimizes the risk of such incidents. In the context of this article, understanding these risks is beneficial in developing a culture of safety.
Advantages of knowing about pressure accidents include improved awareness and preparedness against possible mishaps. However, users must remember that awareness alone is not enough; consistent practices are crucial for safety in any workshop.
Electrical Hazards
Electrical hazards are another significant concern when using air compressors. Electric shock or even fire can result from improperly wired equipment or frayed cords. High-capacity compressors often draw substantial power, increasing the risk of electrical failures. A key characteristic of electrical hazards is their silent nature, as issues may arise without visible signs until a failure occurs.
It is beneficial for users to understand and respect electrical specifications. Unique features of addressing these hazards include installing proper circuit breakers and maintaining equipment regularly. The advantages of proactive measures include enhanced safety and reduced downtime from failures, while disadvantages may include the initial costs involved in upgrading systems.
Preventive Measures
Implementing preventive measures is essential to minimize the risks discussed above. These measures create a safe working environment and ensure that users can operate their air compressors with peace of mind.
Personal Protective Equipment
Personal protective equipment (PPE) is critical for safeguarding individuals working near air compressors. This equipment typically includes safety goggles, gloves, and ear protection. The key characteristic of PPE is its ability to provide a physical barrier against potential injuries. It is a popular choice due to its effectiveness in preventing accidents.
Using PPE has several advantages, such as injury reduction and compliance with safety regulations. However, the disadvantage might be the added cost and the need for maintenance and proper storage to ensure effectiveness.
Safe Operating Procedures
Safe operating procedures outline how to use air compressors properly. These include guidelines on avoiding over-pressurization, regular maintenance checks, and correct shutdown techniques. The key characteristic of these procedures is their structured approach to using machinery safely and efficiently. This is a beneficial choice for any workshop manager serious about safety.
Unique features of established safe operating procedures include step-by-step instructions that can be easily followed. While the advantages include enhanced safety and operational efficiency, the challenge lies in ensuring all staff are well-trained and understand these procedures thoroughly.
"Investing in safety not only protects workers but also enhances productivity and extends equipment life."
To sum up, addressing safety considerations within the context of air compressor usage is vital. Understanding the risks and implementing preventive measures ensures a safe working environment. This approach promotes effective operations and prioritizes the well-being of everyone involved.
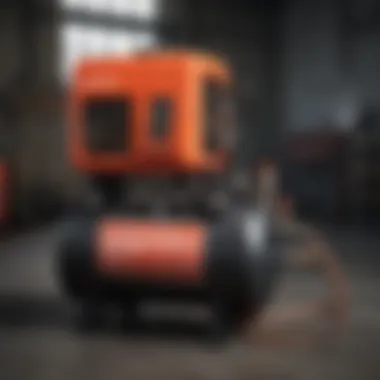
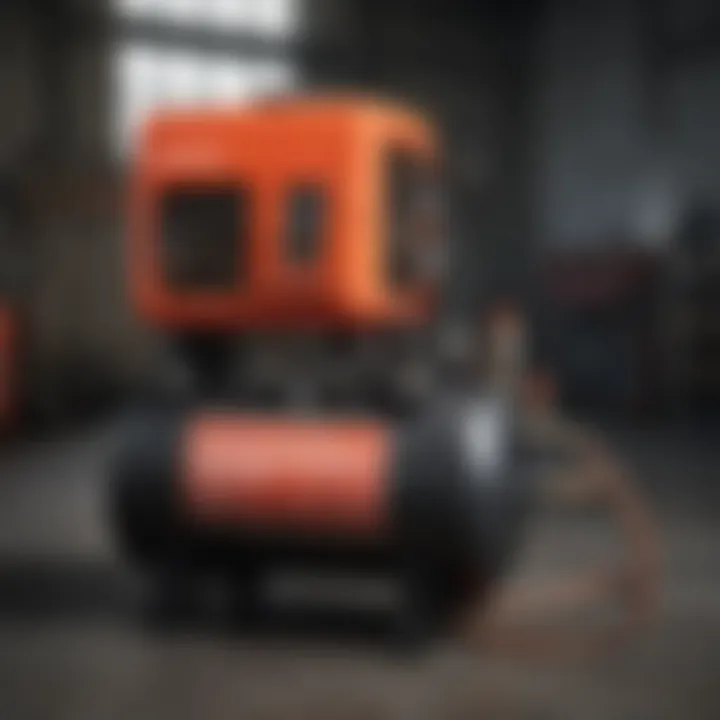
Integration with Shop Equipment
The integration of air compressors with shop equipment is a critical aspect that influences the overall efficiency of any workshop. A well-integrated system ensures that the air compressor operates effectively alongside various tools and machinery. This collaboration can lead to improved productivity, reduced waiting time, and enhanced performance across all operations in the shop. When selecting air compressors, understanding their compatibility with the tools in use is essential.
Air compressors supply compressed air, which is used in various applications including painting, drilling, and powering pneumatic tools. The compatibility between the air compressor and the tools is paramount. Each tool has specific requirements in terms of airflow, pressure, and volume, all of which must align with the air compressorβs output capabilities. This ensures optimal performance and prevents any operational hiccups.
Compressors and Power Tools
The relationship between compressors and power tools is foundational for any shop's functionality. Power tools such as nail guns, impact wrenches, and spray guns rely heavily on compressed air for operation. Understanding the specific air requirements for these tools is crucial. Different tools have different PSI and CFM (Cubic Feet per Minute) requirements, which must be matched to the compressorβs specifications.
Furthermore, using the right compressor ensures that you can maximize the effectiveness of your power tools without risking damage or performance loss. Neglecting this consideration can lead to decreased tool efficiency, premature wear, or even damage to the tools themselves. It is advisable to consult manufacturer specifications for both the tools and the compressor used in conjunction.
Enhancing Efficiency
Streamlining air compressor usage can significantly enhance overall shop efficiency. Two core aspects particularly noteworthy in this regard are air line optimization and storage solutions for tools.
Air Line Optimization
Air line optimization involves strategically organizing and sizing the air delivery system in the shop to minimize pressure drop and maintain consistent airflow. Proper sizing and routing of air lines reduce restrictions that can lead to efficiency losses. The key characteristic of this approach is its ability to maximize the compressor's output at the point of use.
An optimized air line setup can reduce energy consumption and prolong the lifespan of your compressor, making it a popular choice among shop owners. However, one must consider the balance between pipe diameter and overall layout; too large a diameter can lead to higher initial costs without proportional benefits, while too small can restrict flow.
Storage Solutions for Tools
Storage solutions for tools directly contribute to the efficiency of a shop by keeping the workspace organized and improving accessibility. Proper storage methods can facilitate quick access to tools, thus reducing downtime searching for equipment. The key characteristic of effective tool storage is the ability to maintain an organized environment conducive to rapid workflows.
A unique feature of these storage systems is their adaptability; they can be customized according to the specific tools and tasks. However, one possible disadvantage is the upfront investment in quality storage solutions can be significant. Over time, the benefits of increased efficiency and productivity offset initial costs, making them a worthwhile investment for serious shop operations.
Innovative Trends in Air Compressor Technology
In recent years, air compressor technology has seen significant advancements, reflecting the industry's ongoing pursuit for efficiency and performance. Innovative trends are essential for shop owners as they lead to enhanced productivity and reduced operational costs. Understanding these trends helps in making informed decisions about the right equipment, ensuring more effective use of resources.
Energy Efficiency Advancements
Energy efficiency is a primary concern for many industries today. With rising energy costs, air compressors have evolved to become more efficient. Many manufacturers now focus on designs that minimize energy consumption while maximizing output. For instance, variable speed drives allow compressors to adjust their power consumption based on demand, thus reducing unnecessary energy use.
Benefits of adopting energy-efficient models are numerous:
- Lower operating costs: Reduced electricity usage contributes to long-term savings.
- Environmental impact: Increased efficiency means lower carbon emissions, aligning with sustainability goals.
- Improved lifespan: By operating more optimally, components tend to last longer, lowering replacement costs.
Smart Technology Integration
The integration of smart technology into air compressors represents a shift towards a more automated and connected system. This technology offers greater control and monitoring capabilities, which can greatly benefit shop operations.
Remote Monitoring
Remote monitoring systems facilitate real-time performance tracking of air compressors. Through a centralized interface, technicians can view pressure levels, operational status, and even maintenance needs without being on-site. This capability enhances operational oversight and allows for proactive maintenance.
Key characteristic of remote monitoring is its ability to predict failures before they occur, which is a vital consideration for any shop. The main advantages include:
- Early problem detection: Identifying issues sooner prevents smaller problems from escalating.
- Data analytics: Historical data collection helps optimize compressor performance, leading to improved efficiency.
- Compliance: Maintaining records digitally simplifies compliance with regulations.
Automated Controls
Automated controls in air compressors streamline operations and minimize human error. These systems allow for automated adjustments according to workload and environmental conditions. For example, automated shutdown features can kick in during idling to save energy.
One of the main advantages of automated controls is their ease of use. Shop owners can operate compressors without needing extensive training. Furthermore:
- Consistency in performance: Ensures optimal pressure levels are maintained, minimizing fluctuations.
- Increased safety: Reduces the likelihood of accidents by managing compressor operations intelligently.
- Labour savings: Automation allows staff to focus on more critical tasks, yielding higher productivity.
Understanding innovative trends in air compressor technology is crucial for making informed decisions that can drive efficiency and productivity in a shop, ultimately affecting the bottom line.
Finale
Summarizing Key Points
The article has covered multiple facets of air compressors, beginning with a comprehensive overview of their types and functions. Each compressor type has distinct advantages suited for different applications in a shop environment. Additionally, readers were guided through the selection process, including how to assess their needs, budget considerations, and product comparisons. The installation process outlined critical aspects such as site selection, ventilation, and connection setups to ensure safe and effective operation.
Operational guidelines emphasized proper starting and stopping procedures, along with best practices to maintain equipment efficiency. Routine maintenance and troubleshooting provided essential strategies to deal with common issues that might arise. The section on safety considerations was particularly relevant, highlighting the risks associated with compressor use, along with preventive measures to mitigate these hazards.
Future Considerations
Looking ahead, the landscape of air compressor technology is set to evolve significantly, given current trends and innovations.
Sustainability in Air Compression
Sustainability in air compression is now a primary focus in the industry. As environmental concerns rise, compressors that incorporate energy-saving technologies are gaining traction. These systems often feature improved efficiency ratings, which leads to lower energy consumption. Such advancements not only reduce operational costs but also minimize the environmental impact of running compressors. A key characteristic of sustainable compressors is their use of renewable energy sources. This is a beneficial choice for shops eager to lower their carbon footprint while maintaining high operational standards.
The unique features of sustainable air compression systems include variable speed drives that adapt air output as needed. This can help organizations significantly decrease energy waste during idling periods. Nonetheless, potential disadvantages may arise from the higher upfront investment required for these advanced models, although the long-term savings often justify the initial cost.
Potential Developments
Potential developments in air compressor technology hold promising prospects. The integration of smart technology is particularly noteworthy. Smart compressors enable remote monitoring and automated control systems to optimize performance continually. This characteristic is becoming increasingly popular among shops that seek seamless operations and real-time insights.
Unique aspects of these developments include advancements in IoT capabilities, which allow for predictive maintenance based on usage data analysis. The advantages of adopting such technologies include reduced downtime and improved productivity. However, shops must weigh the costs of such technologies against their operational budget and determine the feasibility of implementation, especially for small businesses with limited resources.