Understanding Chicken Hatchery Machines: A Comprehensive Guide
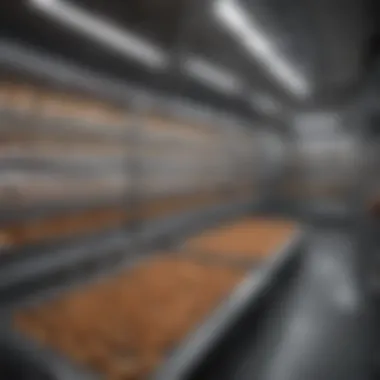
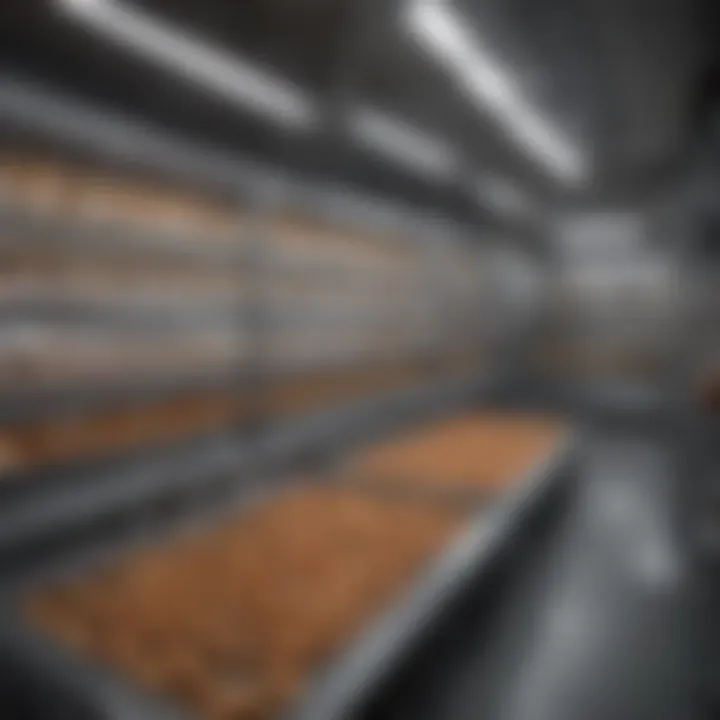
Intro
In the domain of poultry farming, the effectiveness of chicken hatchery machines plays a pivotal role. These machines are not merely tools; they are the backbone of successful poultry operations. A profound understanding of their design and functionality can lead to improved yields and healthier chicks. This guide seeks to explore essential elements surrounding hatchery machines and their impact on modern poultry farming.
Chicken hatchery machines are integral to the incubation process. They are designed to create optimal environmental conditions for eggs to develop and hatch. The evolution of these machines has brought about significant advancements in both technology and productivity. By comprehending various hatchery systems and their specifications, poultry farmers can better manage their operations.
Effective management of these machines addresses common challenges faced in the incubation process. Understanding the key components, such as temperature control, humidity regulation, and air circulation, allows farmers to enhance hatch rates. Moreover, the incorporation of modern technology in these machines is reshaping the landscape of poultry farming.
As we delve deeper, each section will examine specific aspects of chicken hatchery machines in further detail. This includes their types, functionalities, best practices, and technological innovations that are redefining industry standards.
Research and Data Analysis
Understanding the current landscape of chicken hatchery machines requires extensive research and data analysis. This section will explore recent trends and provide statistical insights that emphasize their significance in poultry farming.
Latest Trends in Agriculture and Horticulture
Research has shown that precision agriculture is becoming a leading trend in the farming sector. This trend extends to poultry, where the integration of data-driven technologies enhances hatchery outcomes. By adopting smart systems, farmers can monitor and control several variables throughout the incubation process.
"Efficiency in hatchery operations can be significantly increased through the implementation of data analytics and automated monitoring systems."
Statistical Insights into Hatchery Performance
Statistical data indicates that hatchery efficiency has improved over the years due to advances in machine technology. Some key performance metrics include:
- Hatch Rate: Optimal hatcheries report rates exceeding 80%.
- Energy Efficiency: Newer machines consume less energy while maintaining performance.
- Automation Levels: Machines with high automation reduce labor costs and errors.
These insights help in analyzing the effectiveness of specific hatchery machines and in making informed decisions for future investments.
Best Practices and Techniques
The successful operation of chicken hatchery machines relies on the implementation of best practices. This section discusses effective strategies that can enhance hatchery performance.
Efficient Incubation Management Strategies
It is crucial for farmers to follow efficient incubation management strategies. Some effective techniques include:
- Regular Monitoring: Keep track of temperature and humidity levels.
- Proper Egg Handling: Avoid cracking or damaging eggs before incubation.
- Cleanliness and Maintenance: Ensure machines are clean to prevent disease.
Sustainable Practices in Poultry Farming
Sustainability is becoming increasingly important in the farming industry. Farmers can consider practices like:
- Reduced Waste: Implementing recycling methods for hatchery materials.
- Eco-Friendly Inputs: Utilizing energy-efficient machines to minimize carbon footprint.
These efforts not only improve operational efficiency but also contribute to a healthier environment.
Closure
Prologue to Chicken Hatchery Machines
The realm of poultry farming relies heavily on the efficiency of chicken hatchery machines. Understanding these machines is vital for farmers aiming to optimize the incubation process. These machines have evolved over the years, bringing precision and higher yields to breeding operations. Therefore, a comprehensive grasp of their functions directly impacts the productivity of a hatchery.
Definition of Hatchery Machines
Hatchery machines are devices designed to control the incubation environment for chicken eggs. They simulate the natural conditions required for eggs to develop safely and uniformly. The primary components of these machines include incubators and hatchers. Incubators provide the warm environment necessary for embryo development, while hatchers are used during the final stages before the chicks emerge.
Hatchery machines can range from simple, manual units to advanced, fully automated systems. Their complexity often reflects the scale of the operation they are meant to support. In essence, hatchery machines form the backbone of modern poultry breeding, enabling controlled and predictable hatching cycles.
Importance of Hatchery Machines in Poultry Farming
Hatchery machines are critical in poultry farming for several reasons:
- Enhanced Yield: They create ideal conditions for egg hatching, which increases the percentage of successful hatches. A higher yield translates to better profitability for farmers.
- Time Efficiency: Automated systems reduce the time and labor needed to manage incubation processes. This allows farmers to focus on other essential tasks.
- Quality Control: With precise temperature and humidity regulation, hatchery machines minimize the risks of spoilage and poor development of embryos.
- Scalability: As the demand for poultry products grows, hatchery machines enable farms to expand their operations smoothly without sacrificing quality.
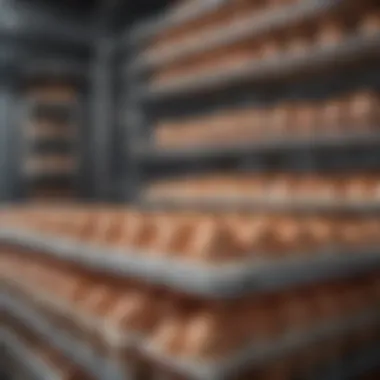
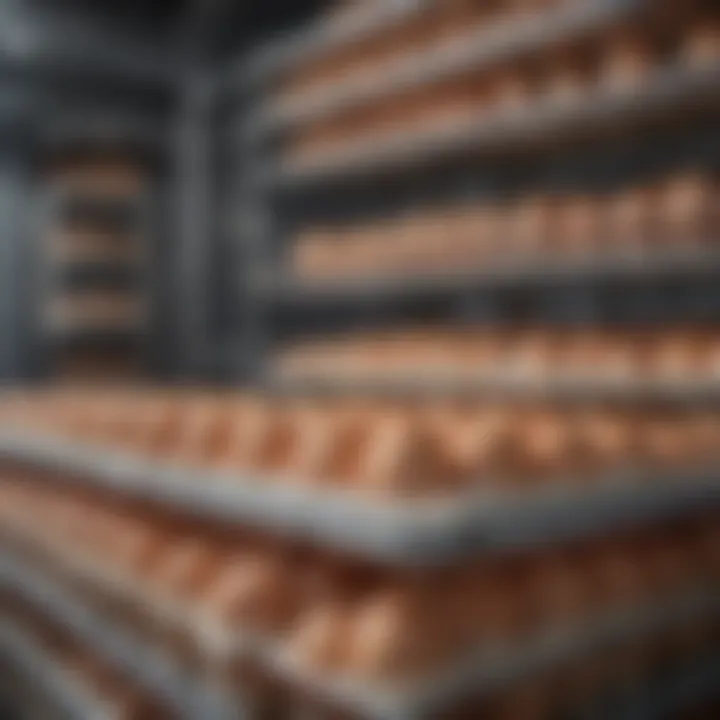
In summary, the understanding of chicken hatchery machines becomes not just a useful skill for those in poultry farming, but a requirement for anyone looking to improve their operational efficiency and output.
Types of Chicken Hatchery Machines
Understanding the different types of chicken hatchery machines is crucial for anyone involved in poultry farming. The effectiveness of these machines greatly influences the success of the incubation process. Each type has unique features designed to meet the specific needs of farmers. Choosing the right machine can enhance chick yield and overall productivity. Moreover, knowing these differences helps in making informed decisions that align with production goals.
Incubators
Incubators are essential devices used to maintain the ideal conditions for egg incubation. They create a controlled environment where eggs can develop into chicks. Most incubators allow for adjustments in temperature, humidity, and ventilation, which are vital for the embryos' growth.
Modern incubators vary considerably. Some models are simple and manually operated. Others boast advanced technology, including automated systems that monitor and regulate conditions.
- Temperature Control: Ideal incubation temperature ranges from 99 to 102 degrees Fahrenheit. Deviations can impact hatching outcomes.
- Humidity Levels: Maintaining 50-55% humidity during incubation ensures proper embryo development.
- Ventilation: Adequate airflow is necessary to supply oxygen and remove carbon dioxide.
The versatility of incubators makes them suitable for small-scale and large-scale operations alike. Farmers should consider their specific needs when selecting incubators to optimize production.
Hatchers
Once the incubation period approaches its end, hatchers become the focal point in the hatching process. Unlike incubators, hatchers are specifically designed for the final days leading up to hatching.
Hatchers must ensure optimal conditions for the eggs as they transition into chicks.
- Temperature and Humidity: While similar to incubators, hatchers often require adjustments in conditions to mimic natural hatching environments.
- Space: Hatching requires more space as the chicks start to move and need room to hatch successfully.
Utilizing hatchers properly can significantly improve hatch rates and chick quality. Their specialized design focuses on creating a suitable atmosphere for the remarkable transformation that occurs during this stage.
Automatic versus Manual Hatchery Machines
The choice between automatic and manual hatchery machines directly affects the operational efficiency of a poultry business. Each option has its pros and cons, and understanding these differences is important.
- Automatic Hatchery Machines: These systems offer significant convenience. They come equipped with temperature and humidity controls, often with alert systems for monitoring conditions. Automation reduces the need for constant supervision, making them ideal for larger operations.
- Manual Hatchery Machines: These machines typically require more hands-on management. Throughout the incubation and hatching process, farmers need to regularly check conditions and make necessary adjustments. While they often cost less initially, they may demand more labor and time, making them suitable for smaller farms or specific situations.
Both types can produce successful outcomes, but selecting the right one will depend on specific operational needs. The balance between automation and manual control can shape the effectiveness of hatchery practices and influence overall productivity.
Key Features of Hatchery Machines
The effectiveness of chicken hatchery machines relies on a variety of key features. These aspects are crucial for ensuring the optimal environment for egg incubation and, ultimately, hatching. The significance of these features cannot be overstated, as they directly influence hatch rates and chick quality. Understanding these elements enhances oneβs ability to choose and operate hatchery equipment effectively. Here are the core components:
Temperature Control
Temperature management is one of the most vital features of hatchery machines. Maintaining the correct temperature throughout incubation is crucial for embryo development. Generally, the ideal temperature range for chicken eggs is around 99.5Β°F to 100Β°F (37.5Β°C to 37.7Β°C). If the temperature is too low, embryos may not develop properly. Conversely, excessive heat can lead to abnormalities or death of the embryos.
Modern hatchery machines offer precise temperature control through thermostats and sensors. Automatic adjustment mechanisms help in minimizing temperature fluctuations, ensuring a stable environment. This is especially important in large-scale operations where batch sizes are significant. Investing in machines with advanced temperature regulation systems can greatly improve hatch outcomes.
Humidity Regulation
Humidity is another critical factor in the incubation process. The appropriate humidity levels help to ensure the correct moisture loss from the eggs and support the overall development of the embryos. Ideally, humidity levels should be around 50% to 60% during the incubation phase and increase to about 70% during hatching.
Hatchery machines equipped with humidistats allow for automatic monitoring and adjustments. This feature is essential as improper humidity can lead to poor hatchability or weak chicks. High humidity may cause sticky chick syndrome, whereas low humidity can lead to shrink-wrapped chicks. Thus, incorporating machines that can effectively regulate humidity is essential for a successful hatchery.
Airflow Management
Airflow management is vital in the incubation environment. Sufficient oxygen levels are required for the developing embryos, while excess carbon dioxide must be expelled. Inadequate airflow can lead to a range of problems, including poor hatching rates.
Many incubators feature fan systems to circulate air evenly. This not only ensures that the temperature and humidity are consistent throughout but also allows for proper gas exchange. Placing emphasis on airflow management, hatchery machines are designed with vents and fans that help maintain optimal conditions. Consistent air movement keeps a uniform environment, which is critical for healthy embryo growth.
Data Monitoring and Logging
The capability for data monitoring and logging is increasingly essential in modern hatcheries. Advanced machines are now equipped with sensors that track various parameters, including temperature, humidity, and airflow. This data can be logged and analyzed over time, allowing hatchery managers to make informed decisions.
This feature assists in troubleshooting potential issues early on. If a parameter deviates from the ideal range, notifications can alert operators, enabling timely interventions. Keeping meticulous records of incubation conditions also aids in improving future hatch cycles. Moreover, this data is crucial for compliance with health and safety regulations and can enhance the sustainability of hatchery operations.
"The careful monitoring and regulation of hatchery conditions lead to better yield and healthier chicks, which directly impacts productivity and profitability in poultry farming."
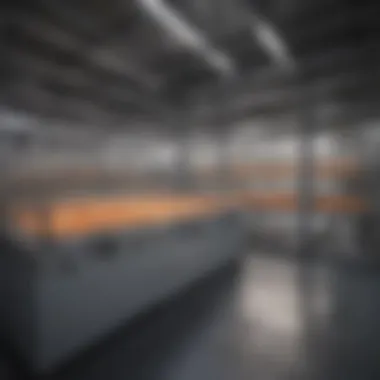
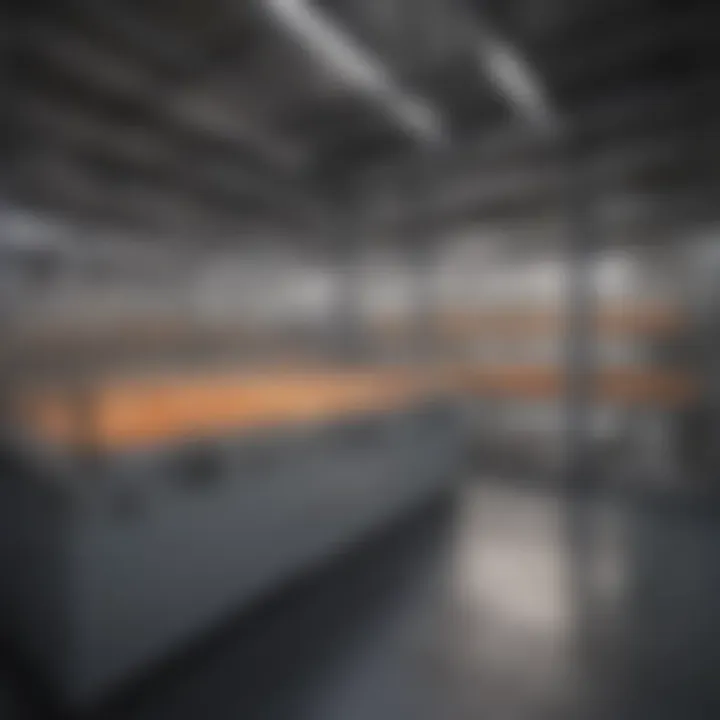
In summary, the key features of hatchery machines significantly influence the success of poultry operations. Focus on effective temperature control, humidity regulation, airflow management, and data monitoring can ultimately lead to improved hatch rates and chick quality. Farmers and hatchery operators must understand these features to optimize their practices.
Understanding the Incubation Process
The incubation process is crucial in poultry farming. It is where eggs develop into healthy chicks. Understanding this process can lead to better management decisions, higher hatch rates, and improved chick quality. This section highlights important steps involved in incubation, such as egg selection and preparation, setting up the hatchery machine, and monitoring the incubation parameters. These elements are all interrelated and essential for optimizing overall hatchery performance.
Egg Selection and Preparation
Selecting the right eggs is the first and most vital step in the incubation process. Fertile eggs from healthy and genetically strong birds ensure a better hatch rate. Look for eggs that have clean, unbroken shells. Freshness is also important; ideally, eggs should be no older than a week when placed in the incubator. Moreover, proper handling and storage conditions can affect the viability of the embryo inside. Store eggs in a cool, humid environment until they are incubated.
Good handling decreases the chances of cracked shells and enhances hatch outcomes.
Setting Up the Hatchery Machine
Before placing eggs in the incubator, setting up the machine correctly is essential. Begin by checking the machineβs functionality to ensure all systems work properly. Temperature and humidity are the critical factors to adjust at this stage. Most hatchery machines require a temperature of 99.5Β°F (37.5Β°C) and humidity levels around 50-55% for optimal incubation. Additionally, ensure the airflow is adequate. It helps carry oxygen and eliminates carbon dioxide, both necessary for embryo development.
- Proper calibration of these settings sets the stage for the successful incubation process.*
Monitoring Incubation Parameters
Once the eggs are in the incubator, constant monitoring is required. It's important to regularly check temperature and humidity levels. A digital thermometer and hygrometer can help with this task. Any fluctuations in temperature or humidity can lead to poor hatch rates or unhealthy chicks. Keep a daily log of these parameters for better analysis of any issues that arise.
Following these steps in understanding the incubation process helps enhance outcomes. With careful attention to detail, poultry farmers can significantly improve the health and viability of the chicks produced through their hatcheries.
Challenges in Operating Hatchery Machines
Operating hatchery machines can present numerous challenges that can affect the efficiency and yield of poultry farming. Understanding these obstacles is essential for anyone involved in this sector. Hatchery machines play a critical role in the incubation of eggs and the overall success of producing healthy chicks. Therefore, recognizing the various challenges allows poultry farmers to implement preventive measures and solutions that enhance operations and productivity.
Effective management of hatchery machines ensures adherence to the required conditions for incubation, thus influencing chick quality. Challenges often arise from both mechanical performance and environmental influences, leading to potential disruptions. This section explores common issues encountered and the impact of environmental factors, enabling farmers to cultivate a more resilient hatchery environment.
Common Issues Encountered
Hatchery machines, like any other technology, are not immune to malfunctions or performance inconsistencies. Common issues can compromise the expected outcomes of the incubation process, resulting in lower hatch rates.
- Temperature Fluctuations: Maintaining optimal temperatures is pivotal. Any sudden change can stress embryos.
- Humidity Control Failure: Insufficient or excessive humidity can lead to dehydration or suffocation of eggs.
- Mechanical Malfunctions: Components such as fans, heaters, and sensors may fail, disrupting the fine balance of necessary conditions.
- Egg Contamination: Poor sanitation practices can lead to the spread of pathogens, jeopardizing the health of the developing embryos.
Being proactive about these challenges will allow a smoother operation and improve outcomes. Regular checks on devices and adherence to routine maintenance are critical in addressing these problems.
Impact of Environmental Factors
Environmental factors play a crucial role in the success of hatchery operations. These factors can vastly differ based on the location, season, or even specific setups within hatcheries. Understanding their influence helps farmers prepare for variability and safeguard their investments.
- Temperature Variations: Ambient temperature changes can disrupt controlled environments, impacting the incubation process. Warm months may require additional cooling solutions while cold months require increased heating.
- Humidity Levels: External weather conditions can lead to unexpected humidity levels inside the hatchery if not managed correctly.
- Infrastructure and Location: The physical space of the hatchery can affect ventilation and heat retention. Suboptimal locations, such as near high-traffic areas or poorly insulated buildings, can compromise incubator performance.
Farmers should regularly assess environmental conditions, employing tools for real-time monitoring. Effective management that addresses these factors not only enhances chick quality but also contributes to sustainable cultivation, ultimately leading to more successful hatchery operations.
"Investing in quality machines and understanding environmental factors is vital for maximizing hatchery efficiency."
By identifying and addressing these challenges, poultry farmers can take significant steps toward improving their machinery management, ensuring higher hatch rates and healthier chicks.
Maintenance of Hatchery Machines
The maintenance of hatchery machines is crucial for ensuring optimal performance and longevity of these essential tools in poultry farming. Proper maintenance practices not only enhance the efficiency of the machines but also significantly reduce the incidence of operational failures. It is vital to acknowledge that the condition of hatchery machines directly impacts the health and viability of the chicks produced. Therefore, a systematic approach to maintenance is a priority for poultry farmers aiming for high productivity.
Regular upkeep of these machines fosters consistent incubation conditions. This consistency is important as it influences temperature control, humidity regulation, and airflow managementβkey factors that determine the success of the incubation process. Effective maintenance practices also lower energy consumption, contributing to cost savings in the long run. Therefore, prioritizing maintenance is not merely about extending the life of machinery; it is an integral aspect of overall farm management.
Routine Maintenance Practices
Routine maintenance practices form the foundation of an effective maintenance strategy. These practices should be integrated into the daily or weekly routines of poultry operations to ensure consistent machine functionality.
- Cleaning: Regularly clean the hatchery machines to prevent the buildup of dust and bacteria, which can affect the hatch rate. Pay special attention to trays, incubators, and humidifiers.
- Calibration: Check and calibrate temperature and humidity controls to ensure precise readings. Accurate measurements are vital for the health of eggs during incubation.
- Inspection: Conduct visual inspections of all machine components. Look for signs of wear, frayed wires, or any components that might need repair or replacement.
- Updating Software: If your hatchery machines utilize smart technology, ensure that the software is up to date, optimizing the performance of monitoring systems and alarms.
- Lubrication: Apply lubricant to moving parts as recommended by the manufacturer to reduce friction and wear.
By establishing a schedule for these routine practices, poultry farmers can mitigate issues before they escalate into costly repairs.
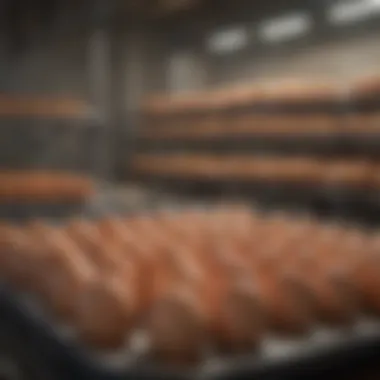
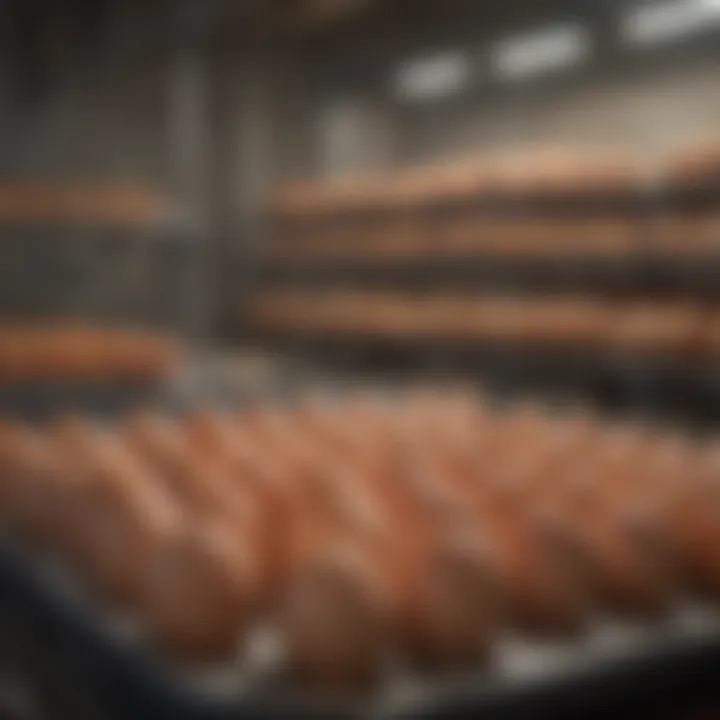
Troubleshooting Common Problems
Despite regular maintenance, challenges can still arise with hatchery machines. Recognizing and troubleshooting common problems is essential for minimizing downtime.
- Temperature Fluctuations: If the machine experiences erratic temperature changes, check the thermostat and the heating elements. Ensure that sensors are functioning properly and are not obstructed by debris.
- Humidity Issues: Inadequate humidity can lead to poor hatch rates. If humidity levels are not stabilizing, inspect the water supply lines and the humidifier. Make sure they are clean and functioning.
- Power Failures: Unplanned power outages can disrupt incubation. Utilizing an uninterruptible power supply (UPS) can safeguard against this issue. Regularly check the backup systems to ensure they are operational.
- Airflow Obstacles: Reduced airflow can create a challenging environment in the incubator. Inspect vents and filters to ensure they are not blocked and are free of obstructions.
By addressing these common problems promptly, poultry farmers can maintain the efficiency of their hatchery operations and ensure a favorable environment for egg incubation.
"Regular maintenance not only prolongs the life of hatchery machines but also directly influences the success of poultry farming practices."
Technological Advancements in Hatchery Machines
Technological advancements shape the efficiency and productivity of chicken hatchery machines significantly. Innovations in this field have allowed poultry farmers to optimize their operations while reducing labor and minimizing errors. With the ongoing evolution of technology, new systems emerge that enhance precision and reliability in the incubation and hatching processes. Understanding these advancements is crucial for modern poultry practices, as it impacts the overall output and sustainability of hatcheries.
Automated Incubation Systems
Automated incubation systems are a major leap forward in hatchery technology. These systems eliminate many manual tasks associated with egg incubation. By automating temperature and humidity controls, farmers can ensure a more stable environment for the developing embryos.
- Key Benefits:
- Reduced labor costs due to decreased need for manual monitoring.
- Increased consistency in incubation conditions, leading to better hatch rates.
- Ability to manage large volumes of eggs efficiently.
Farmers utilizing automated systems often report fewer instances of human error, which can adversely affect incubation success. Sensors and software work together to track critical parameters, providing real-time data that aids in making informed decisions for optimal hatching conditions.
Smart Monitoring Technologies
Smart monitoring technologies represent another significant development in the hatchery sector. These systems utilize IoT (Internet of Things) capabilities to connect hatchery machines to the internet. Users can monitor conditions from remote locations, offering greater control and accessibility.
- Advantages of Smart Monitoring:
- Real-Time Alerts: Farmers are promptly informed of any deviations from set parameters via mobile devices.
- Data Analysis: The ability to track historical data patterns can guide future improvements in incubation processes.
- Integration with Other Systems: Smart technologies can often connect with feed systems, health monitoring tools, and environmental controls for a holistic approach to poultry management.
By adopting smart monitoring technologies, poultry farmers not only enhance operational efficiency but also contribute to better resource management, ultimately translating to increased profitability.
Best Practices in Hatchery Management
Effective hatchery management is crucial for ensuring high-quality chick production and operational efficiency. By prioritizing best practices, poultry farmers can significantly enhance their productivity and profitability. This section highlights key strategies that can be implemented in hatchery management, discussing specific elements, benefits, and important considerations.
Optimizing Incubation Conditions
Optimizing incubation conditions is one of the most critical aspects in hatchery management. To achieve strong hatch rates and healthy chicks, several factors must be maintained at ideal levels. This includes temperature, humidity, and ventilation.
- Temperature Control: The ideal incubation temperature typically ranges from 37.5 to 38.5 degrees Celsius. Keeping this within range is vital. Slight fluctuations can lead to poor embryo development or even embryo death.
- Humidity Levels: Generally, humidity should be around 50-55% for the first 18 days. During the last few days, this should rise to about 65-70% to facilitate proper hatching. Monitoring humidity is essential to prevent dehydration or excessive moisture.
- Airflow Management: Proper airflow ensures that the eggs receive adequate oxygen while removing carbon dioxide. This encourages healthy embryo development.
Regular monitoring and adjustments can be made with the help of integrated data logging systems in modern hatchery machines. By frequently checking these parameters, farmers can quickly respond to deviations from optimal levels, optimizing the chances of successful hatches.
Enhancing Chick Quality and Survival Rates
Enhancing chick quality and survival rates is another fundamental goal of hatchery management. Various strategies can be implemented to ensure that chicks are healthy and vigorous at the point of hatching.
- Genetic Selection: Using high-quality breeding stock can significantly impact the overall quality of the chicks. Selecting chicks from genetically superior lines leads to stronger, healthier offspring.
- Handling Practices: Minimizing stress during handling is essential. Stress can reduce survivability. Care should be taken during transport and transfer processes.
- Nutrition and Early Feeding: Providing adequate nutrition during the critical early days boosts the immune systems of chicks. This can lead to higher survival rates, especially in the first few weeks post-hatching.
- Monitoring Health Indicators: Conducting regular health assessments of newly hatched chicks is vital. Monitoring for signs of illness or distress can allow for rapid response, improving ultimately the overall survival rates.
"Implementing these practices leads to a remarkable improvement in chick quality, translating into better performance in the grow-out phase."
Epilogue
In this article, we explored the intricate world of chicken hatchery machines and the pivotal role they play in modern poultry farming. Understanding these machines provides not only operational efficiency but also enhances the viability of poultry production. The conclusion serves as an important recap of the essential points covered, highlighting how these machines optimize the incubation process and ultimately influence the outcome of the hatch.
Future Trends in Hatchery Technology
Looking ahead, the landscape of hatchery technology is poised for significant evolution. Innovations such as artificial intelligence and machine learning are being integrated into hatchery machines. These advancements will facilitate real-time data analysis, improving decision-making in incubation parameters. Moreover, energy-efficient designs are being developed. These designs not only reduce operating costs but also address environmental concerns. As a result, poultry farmers can achieve better yields while minimizing resource consumption.
The Role of Hatcheries in Sustainable Poultry Practices
Hatcheries are increasingly recognized for their contribution to sustainable poultry farming. By employing effective management practices and adopting advanced technologies, hatcheries can enhance chick quality and improve survival rates. Sustainable practices also include reducing waste and utilizing renewable energy sources. This shift not only benefits the environment but also supports the economic viability of poultry farms. It is essential for poultry farmers to understand the importance of aligning their operations with sustainability goals to meet consumer demands and regulatory standards.
"Sustainable poultry practices are not just a trend; they are essential for the future of agriculture."
As we have discussed, understanding chicken hatchery machines encompasses multiple facets. From technology advancements to sustainability initiatives, the elements we highlighted offer a comprehensive view for poultry farmers and industry stakeholders. These insights empower them to make informed decisions, thereby enhancing their operational effectiveness and contributing to a robust agricultural future.