Understanding Hydraulic Hammer Grease: Applications and Best Practices
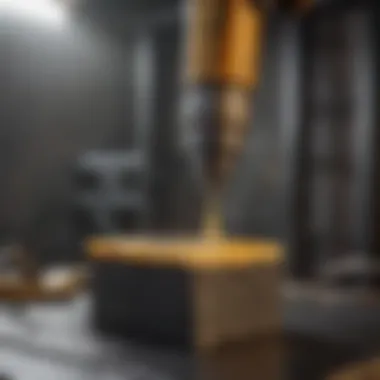
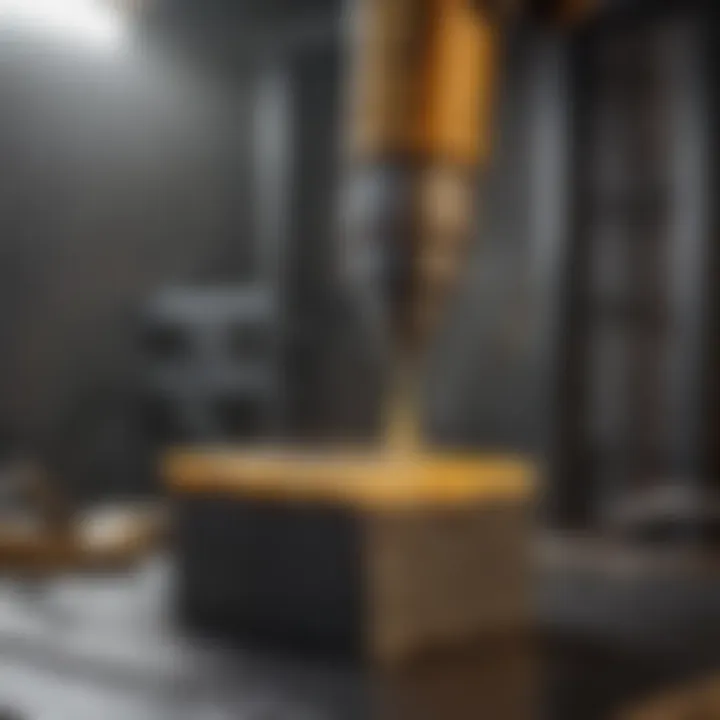
Intro
Hydraulic hammer grease serves an essential role in the smooth operation and longevity of hydraulic hammers used in construction and demolition. The efficient performance of these hammers depends heavily on the quality and proper application of their grease. This article examines crucial elements surrounding hydraulic hammer grease, from the various types available to their applications and best practices for maintenance. Understanding these factors not only enhances performance but also extends the lifespan of hydraulic systems in various sectors, particularly in agriculture and construction.
Research and Data Analysis
Analyzing the role of hydraulic hammer grease requires an understanding of current trends in machinery usage within the agricultural and construction industries. Efficient machinery operation is paramount in optimizing workflows, and this includes how machinery is maintained.
Latest Trends in Agriculture and Horticulture
In modern agriculture, there is a growing emphasis on sustainability and efficiency. Equipment that operates reliably is essential for maximizing production. Hydraulic hammers, utilized for tasks such as breaking concrete or driving piles, must function optimally. Therefore, selecting the appropriate hydraulic hammer grease becomes critical. The lubrication needs vary according to the specific machinery and environmental conditions in which they operate.
Statistical Insights into Performance and Durability
Recent studies indicate that proper lubrication can significantly increase the lifespan of hydraulic machinery. For instance, equipment that adheres to proper grease application protocols sees a performance efficiency increase of up to 25%. This is crucial for minimizing downtime and maintenance costs. Therefore, using quality hydraulic hammer grease is no longer an option but a necessity for agricultural and construction professionals.
Best Practices and Techniques
To achieve optimal performance with hydraulic hammers, a few best practices regarding grease application should be followed. Below are techniques that can help maintain machinery effectively.
Efficient Machine Maintenance Strategies
- Regular Inspections: Conduct routine checks on hydraulic hammer systems to ensure there are no leaks or signs of inadequate lubrication.
- Grease Selection: Choose grease based on the manufacturer's specifications considering operating temperature, load conditions, and climate.
- Consistent Application: Ensure that grease is applied consistently, paying attention to areas that experience frequent friction.
Sustainable Maintenance Techniques
- Recyclable Greases: Look for environmentally friendly lubricants that minimize waste and are easy to dispose of.
- Training and Education: Equip staff with knowledge on proper lubrication techniques and the importance of hydraulic hammer grease.
Challenges and Solutions
One notable challenge faced in applying hydraulic hammer grease is identifying the right product for specific conditions. Making an informed decision can prevent machinery failure and ensure effective operation.
"Choosing the correct hydraulic hammer grease directly impacts equipment performance and maintenance costs."
It's advised to consult machinery manuals and engage with suppliers who can provide recommendations based on usage requirements. Additionally, staying updated with innovations in lubrication technology is essential for long-term success.
By understanding these elements of hydraulic hammer grease, professionals in agriculture and construction can better optimize their machinery's performance and operational efficiency.
Intro to Hydraulic Hammer Grease
Hydraulic hammer grease plays a pivotal role in the operation and longevity of hydraulic hammers, which are essential in construction and demolition industries. These hammers exert immense force, making the selection and application of the right grease critical for both performance and equipment health.
Choosing the correct grease not only ensures the hydraulic hammer functions effectively but also enhances safety during operations. Proper lubrication minimizes wear and tear, reduces friction, and ultimately contributes to a more efficient work process. Moreover, understanding hydraulic hammer grease is equally important for agricultural professionals who may employ similar hydraulic systems in their equipment.
As we delve into the specific elements of hydraulic hammer grease, it is vital to consider its definition and purpose, along with its role within hydraulic systems. This foundational knowledge will enable professionals to make informed decisions about lubrication strategies, enhancing performance and extending equipment life.
Definition and Purpose
Hydraulic hammer grease is a specialized lubricant designed specifically for use in hydraulic hammers. Its primary purpose is to reduce friction and wear between internal moving parts, ensuring efficient operation of the hydraulic mechanism. Grease acts as a barrier, protecting these components from corrosion and the elements, thereby prolonging the equipment's lifespan.
This grease is formulated to withstand the extreme pressure and dynamics present in hydraulic systems. The right grease will maintain its consistency even under varying temperatures and heavy loads, ensuring that critical components operate smoothly. Not all greases are suitable for every application, which emphasizes the need to understand the specific requirements of hydraulic hammer grease.
Role in Hydraulic Systems
In hydraulic systems, the role of grease extends beyond mere lubrication. It maintains hydraulic fluid viscosity and helps keep contaminants at bay. By ensuring that the hydraulic hammer operates at optimal efficiency, the grease contributes to other benefits, including:
- Friction Reduction: Proper lubrication decreases wear on moving parts and prevents overheating.
- Energy Efficiency: Reduced friction allows for better energy utilization, which can lead to lower operational costs.
- Resistance to Extreme Conditions: Hydraulic hammer grease is designed to perform well in various environmental conditions, including both hot and cold temperatures.
In summary, hydraulic hammer grease is an integral component in hydraulic systems, ensuring not just functionality but also enhancing overall performance. Understanding its definition and role sets the stage for discussing types, applications, and guidelines for effective maintenance in later sections.
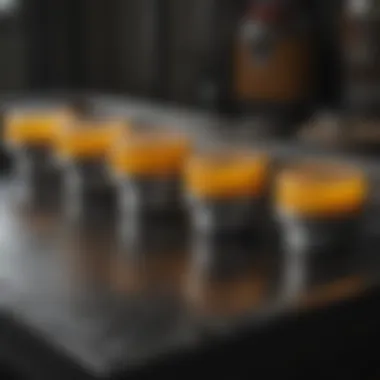
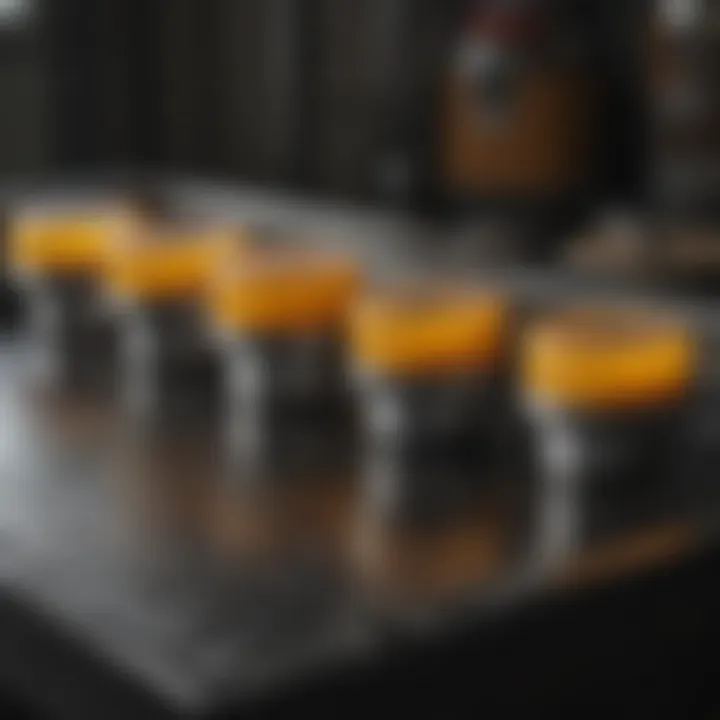
Types of Hydraulic Hammer Grease
Understanding the types of hydraulic hammer grease is essential to ensure the optimal performance of hydraulic systems. The choice of grease affects factors such as lubrication efficiency, equipment longevity, and protection against wear and corrosion. Each type of grease has unique properties and applications, which makes it significant to match the appropriate grease with the specific requirements of the equipment being used.
Lithium-Based Grease
Lithium-based grease is one of the most common types used in hydraulic hammer applications. This grease is known for its excellent adhesion and stability under high pressure. It resists water washout and provides good temperature stability, making it suitable for a wide range of environmental conditions.
Key benefits include:
- High load-bearing capacity: This type of grease can withstand strong pressures, which is crucial for hydraulic systems.
- Oxidation stability: It maintains its performance over time, extending the intervals between lubrication.
- Compatibility: Lithium grease merges well with various lubricant compositions, which is beneficial for those using mixed lubricants.
However, it also has limitations. For instance, it may not perform well in extremely high temperatures, which could lead to grease breakdown.
Calcium-Based Grease
Calcium-based grease provides another option, often used in environments that require water resistance. This type is characterized by its ability to make a stable emulsion with water, providing effective lubrication even in wet conditions.
Advantages include:
- Water resistance: It offers superior protection against moisture, which is crucial for outdoor applications.
- Environmentally safe: This grease is typically non-toxic, making it suitable for agricultural settings.
Nevertheless, calcium grease has some drawbacks. It can have lower high-temperature performance compared to lithium-based greases, and its compatibility with synthetic oils can be limited. Users must be cautious when selecting this type to avoid operational issues.
Synthetic Grease
Synthetic grease represents an advanced option and is designed for high-performance applications. These greases can be formulated for specific operating conditions, often leading to better performance than traditional options. They provide exceptional oxidation resistance, wear protection, and stability at various temperatures.
The benefits of synthetic grease include:
- Versatility: It can be tailored to meet various operational demands, which can enhance system efficiency.
- Longer service intervals: Due to advanced formulations, synthetic greases can extend lubrication intervals significantly, reducing maintenance frequency.
- Wide temperature range: They work effectively across a broader range of temperatures, making them ideal for extreme conditions.
On the flip side, synthetic greases can come at a higher cost. Their specific advantages must be weighed against the project budget and expected performance.
By understanding these types of hydraulic hammer greaseβlithium-based, calcium-based, and syntheticβusers can make informed choices that enhance the performance and reliability of their hydraulic systems.
Importance of Proper Lubrication
Proper lubrication plays a critical role in the performance and reliability of hydraulic hammers. Without appropriate lubrication, these heavy machines can encounter significant issues that could lead to costly repairs and downtime. Hydraulic hammer grease acts as a barrier, minimizing friction and wear among moving parts. This protection is essential not only for the longevity of the equipment but also for maintaining operational efficiency.
Reducing Friction
Friction is an inherent factor in any mechanical system, particularly in hydraulic systems. The movement of metal parts against one another generates heat and wear. This is where hydraulic hammer grease comes into play. By forming a protective film on metal surfaces, it reduces direct contact between them. Consequently, this minimizes friction.
An effective grease facilitates smooth movement and operates under various conditions. Grease also compensates for thermal expansion. Different types of grease may be used depending on the operating conditions. Properly chosen grease can greatly decrease wear, enhancing the hydraulic hammer's overall performance.
Extending Equipment Life
One of the main benefits of employing hydraulic hammer grease correctly is the extension of equipment life. By reducing friction, the grease not only protects the moving parts but also diminishes the likelihood of overheating. Overheating can lead to considerable damage or even complete failure of hydraulic components.
Investing in quality grease and maintaining a proper lubrication schedule can significantly prolong the lifespan of hydraulic hammers. This can translate to fewer replacements or repairs. For operators, understanding the right type of grease and its application frequency can lead to savings in maintenance costs, ensuring a more productive work environment.
Preventing Corrosion
Corrosion is a common threat to hydraulic systems, particularly in environments exposed to moisture or chemicals. Proper lubrication with hydraulic hammer grease creates a barrier that can protect metal components from these corrosive elements. Grease often contains additives that enhance this protective action. As a result, parts stay cleaner and are less susceptible to rust and corrosion.
Incorporating correct lubrication practices can prevent long-term damage caused by oxidation or chemical reactions. Regular inspections can help ensure that the grease remains effective, protecting the equipment over time.
Proper lubrication is not just a convenience; it is an operational necessity that protects assets and prolongs their useful life.
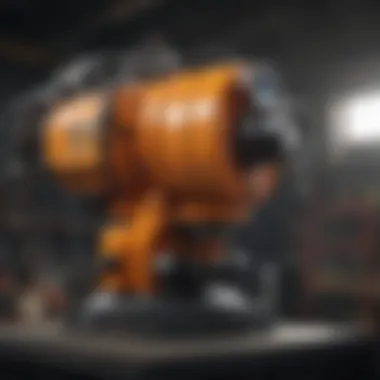
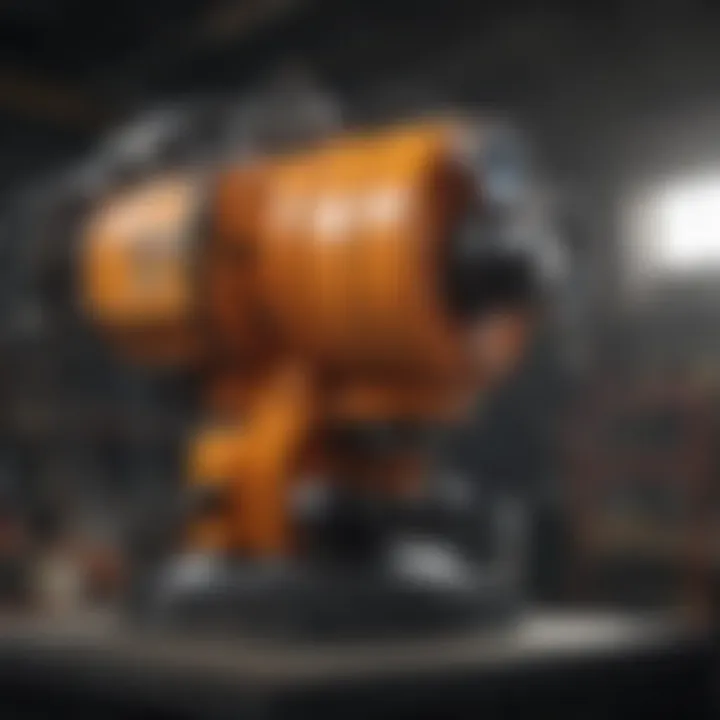
In summary, proper lubrication using hydraulic hammer grease is essential. It reduces friction, extends the life of equipment, and prevents corrosion. For agriculture farmers and construction professionals, applying the right grease at scheduled intervals is a smart investment in the longevity and efficiency of their hydraulic systems.
Application Guidelines
In the realm of hydraulic hammer grease, the application guidelines play a pivotal role. Proper application not only enhances the performance of hydraulic systems but also ensures that equipment operates at optimal efficiency. The choice of grease and the method of application directly affect the longevity and efficiency of hydraulic hammers. This section explores how to identify suitable grease, determine the frequency of application, and the necessary tools for effective lubrication.
Identifying Suitable Grease
Selecting the right grease is essential for ensuring the effectiveness of hydraulic hammers. Not all greases are created equal, and choosing one that meets the specific needs of the hydraulic equipment can have a significant impact on performance.
A few key factors to consider include:
- Compatibility with Equipment: Each hydraulic hammer may require a specific type of grease as advised by the manufacturer. Using the wrong grease can lead to malfunction or premature wear.
- Operational Environment: The conditions under which the hydraulic hammers operate can dictate the type of grease needed. For example, high-temperature environments may require greases with enhanced thermal stability.
- Additives: Some greases contain additives to improve performance in certain situations, such as anti-wear agents and corrosion inhibitors. Understanding these components can help in selecting the appropriate grease for your application.
Application Frequency
Knowing how often to apply grease is critical for maintaining hydraulic system efficiency. Over-lubrication can lead to grease contamination and potential failure, while under-lubrication can increase wear and decrease performance.
Here are a few guiding principles to determine application frequency:
- Manufacturer Recommendations: Always defer to the recommendations provided by the hydraulic hammer manufacturer. They offer specific guidance on when and how often to lubricate the equipment.
- Operational Hours: For equipment used frequently, consider greasing after a set number of operational hours. A common guideline is to check grease levels every 10 to 20 working hours.
- Monitoring Performance: Observing the behavior of your hydraulic hammer can provide insight into lubrication needs. If there is increased noise or vibrations, it might be time to recheck the lubrication.
Tools for Application
The tools used for applying hydraulic hammer grease can affect the efficiency and effectiveness of the process. Using the right tools ensures that the grease is delivered accurately and efficiently, minimizing waste.
Common tools for application include:
- Grease Guns: These are essential for delivering grease to specific points on hydraulic hammers. Manual, pneumatic, and electric grease guns are available, depending on the volume of grease required and the context of use.
- Grease Fittings or Zerks: Ensuring that the hydraulic hammer has appropriate grease fittings installed is crucial for easy access during lubrication.
- Quality Control Tools: Consider utilizing tools to monitor the grease condition, such as grease testers that can offer insights into the consistency and effectiveness of the grease in use.
Proper lubrication practices not only improve hydraulic hammer performance but also enhance overall equipment longevity and productivity.
Challenges in Hydraulic Hammer Grease Selection
Choosing the right hydraulic hammer grease involves various challenges that professionals must carefully navigate. The correct selection is essential not only for immediate performance but also for the long-term sustainability of hydraulic systems. Understanding viscosity, temperature resistance, and environmental factors can lead to informed decisions that enhance the functionality of hydraulic equipment.
Viscosity Issues
Viscosity describes a fluid's resistance to flow. In hydraulic hammer grease, it significantly influences lubrication efficiency. The right viscosity ensures optimal performance by forming a protective film between moving parts. If the grease is too thick, it can impede flow, leading to insufficient lubrication. Conversely, grease that is too thin may fail to provide adequate protection, causing wear and tear.
- Optimal Viscosity: Consider the manufacturer's specifications when selecting grease. Many manufacturers recommend a specific viscosity grade for their hydraulic systems.
- Temperature Influence: Viscosity can change with temperature fluctuations. Ensuring that the chosen grease maintains its viscosity across varying temperatures ensures reliable operation.
- Testing Viscosity: Regular testing of grease viscosity can help in detecting performance issues before they lead to equipment failure.
Temperature Resistance
Hydraulic hammer grease must withstand varying temperatures without breaking down. Different applications may expose the grease to both high and low temperatures, affecting its performance. Grease that lacks adequate thermal stability can oxidize, leading to sludge formation and reduced lubrication efficacy.
- High-Temperature Challenges: Greases must resist degradation at elevated temperatures typical of hydraulic systems under load. Choosing products specifically formulated for high-temperature resistance is imperative.
- Low-Temperature Challenges: In colder environments, greases should remain fluid enough to provide effective lubrication upon startup. Consideration of the pour point is essential in these cases.
- Manufacturer Guidelines: Referring to guidelines from grease manufacturers can help in selecting the right product with suitable temperature ratings.
Environmental Considerations
The environmental impact of hydraulic grease is an important aspect not only from a regulatory perspective but also for sustainable operational practices. It is essential to comprehend how grease impacts both equipment and surroundings.
- Biodegradable Options: The current trend leans toward greases that are biodegradable. These products minimize adverse effects on the environment during accidental spills or leaks.
- Waste Management: Proper disposal methods for used hydraulic greases reduce environmental risks and comply with local regulations.
- Compliance with Regulations: Understanding the relevant regulations governing hydraulic grease usage, such as those from environmental agencies, helps in selecting compliant products.
In summary, selecting the correct hydraulic hammer grease is complicated by viscosity issues, temperature resistance, and environmental regulations. Familiarity with these challenges equips agricultural and construction professionals with the knowledge needed to make informed lubrication choices.
Maintenance Best Practices
The significance of maintenance best practices in relation to hydraulic hammer grease cannot be overstated. Proper maintenance ensures that hydraulic systems function optimally, mitigating risks, enhancing durability, and ultimately leading to cost savings. Neglecting maintenance can result in increased wear on equipment, reduced efficiency, and potential system failures.

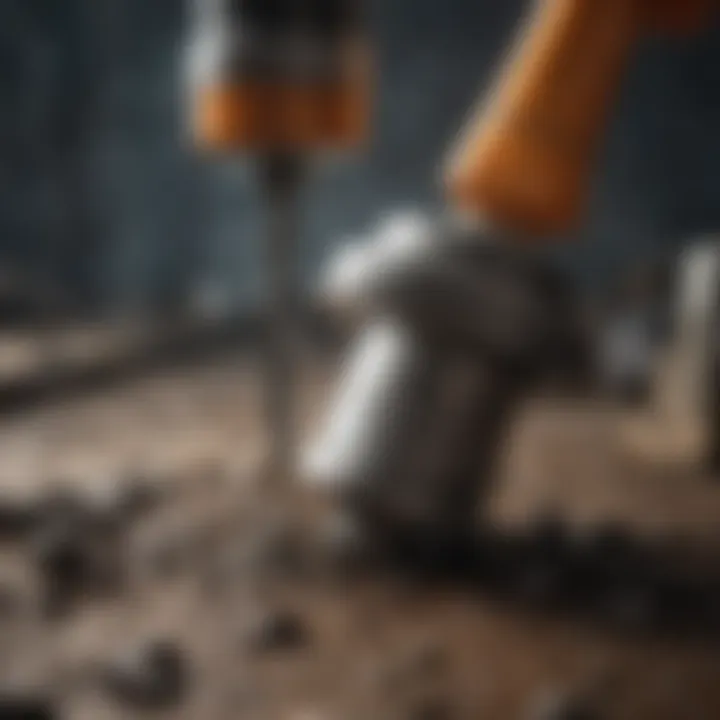
Regular and systematic maintenance contributes to maximizing the lifespan of hydraulic hammers. By establishing effective maintenance routines, operators can greatly reduce the occurrence of breakdowns, which often incur significant downtime and excessive repair costs. Moreover, a well-maintained system operates more efficiently, translating into lower energy consumption and better performance.
In this section, we will explore key practices that ensure hydraulic hammers function effectively over time. These practices include regular inspections, cleaning procedures, and monitoring performance. Each element is vital in sustaining the health of hydraulic hammers, a critical aspect in construction and demolition work.
Regular Inspections
Regular inspections are crucial for identifying potential issues before they escalate into significant problems. They help in evaluating the state of hydraulic systems and the condition of the grease being used. During inspections, operators should check for:
- Sign of wear and tear on components.
- Integrity of hoses and seals.
- Grease leakage or contamination.
- Performance of lubrication systems.
By conducting inspections routinely, operators can adjust application methods, addressing any adverse conditions that may impact system performance. Early discovery of issues often leads to simpler and less costly repairs. It is advisable to maintain detailed records of inspections, which helps in tracking performance trends and highlights areas needing attention.
Cleaning Procedures
Cleaning the hydraulic hammer and its components is essential in maintaining optimal performance. Contaminants and debris can enter the system, affecting the grease's efficacy and possibly leading to breakdowns. Effective cleaning procedures include:
- Removing old grease thoroughly to prevent mixing with new grease, which can dilute the lubricant's effectiveness.
- Using appropriate solvents that do not harm the hydraulic system, ensuring that all residues are eliminated.
- Inspecting and cleaning filters to ensure they are free from blockages or build-up.
Cleaning should be conducted in accordance with the manufacturer's guidelines. Following prescribed methods assures that the hydraulic hammer remains in good working order and reduces the risk of contamination. Keeping components clean enhances the performance and efficiency of hydraulic systems.
Monitoring Performance
Monitoring performance is an ongoing task that enables operators to analyze the effectiveness of the lubrication strategy in place. Regular validation helps in determining if the hydraulic hammer is functioning as expected. Key aspects to monitor include:
- Levels of grease consumption.
- Operating temperature during use.
- Noise levels and vibrations while in operation.
- Response time of hydraulic functions.
Operators can utilize various tools and technologies to measure these indicators. Identifying abnormalities quickly can facilitate timely interventions, ensuring that any deviation from expected performance is addressed promptly. A well-monitored system is far less likely to encounter severe issues, translating into greater operational reliability.
Maintaining hydraulic hammers through inspections, cleaning, and performance monitoring is not just a requirement; it is an investment in efficiency and reliability.
Regulatory Standards and Compliance
Understanding the regulatory standards associated with hydraulic hammer grease is essential for ensuring compliance, safety, and optimal performance in hydraulic systems. These regulations guide manufacturers and users in selecting and applying grease that meets specific industry benchmarks. This section will outline key industry regulations that govern the use of hydraulic hammer grease as well as safety considerations that must be adhered to in order to minimize risks associated with improper lubrication practices.
Industry Regulations
Industry regulations play a critical role in the formulation and usage of hydraulic hammer grease. These regulations often stem from national and international bodies aimed at ensuring effective and safe operation of hydraulic systems. Some relevant standards include:
- ISO 6743: This standard categorizes lubricants, including greases, based on performance and safety characteristics. Hydraulic hammer grease must comply with these standards to ensure reliability under various working conditions.
- ASTM D4950: This specification outlines the requirements for grease used in various industrial applications. Adherence to this specification ensures that the grease can withstand high pressures and temperatures while maintaining its protective properties.
- EPA Regulations: Environmental Protection Agency regulations address environmental impacts associated with grease disposal and adherence to eco-friendly practices. The use of biodegradable greases is encouraged to protect the environment.
Compliance with these regulations not only enhances performance but also provides reassurance to users that their hydraulic systems are optimized for safety and efficiency. Violating these standards can lead to equipment malfunction, increased wear, and potentially harmful environmental effects.
Safety Considerations
In the context of hydraulic hammer grease, safety considerations encompass both the handling of the grease and the operational practices surrounding hydraulic systems. Important factors to keep in mind include:
- Material Safety Data Sheets (MSDS): Always refer to the MSDS for the specific grease used. This document provides vital information on hazards, handling practices, and first-aid measures.
- Personal Protective Equipment (PPE): When applying grease, it is crucial to wear appropriate PPE such as gloves and goggles to prevent skin and eye contact. Exposure to greasy substances can lead to adverse health effects, so proper precautions are necessary.
- Proper Storage: Grease should be stored according to vendor specifications to prevent contamination or degradation. Incorrect storage may render the grease ineffective, putting hydraulic systems at risk.
- Best Application Practices: Following recommended application methods minimizes the risk of over-application, which can lead to leaks and environmental hazards.
"Adhering to industry regulations and safety considerations is not just a formality; it is a best practice that protects both individuals and equipment."
Incorporating these regulatory and safety elements into the routine maintenance of hydraulic systems fosters a safe and compliant working environment. Ultimately, understanding these guidelines helps users make informed decisions, leading to more efficient operations and longevity of hydraulic hammer systems.
The End
Summary of Key Points
- Definition and Purpose: Hydraulic hammer grease is essential for lubricating components in hydraulic hammers, allowing for efficient operation.
- Types of Grease: Various types, including lithium-based, calcium-based, and synthetic greases, cater to different needs and operating conditions.
- Proper Lubrication: Regular lubrication is fundamental to reducing friction, extending the lifespan of machinery, and preventing wear and tear.
- Application Guidelines: Knowing how often and which tools to use during grease application ensures equipment operates optimally.
- Challenges: Understanding viscosity issues and environmental factors helps in selecting the right grease.
- Maintenance Best Practices: Routine checks and cleaning procedures enhance performance and safety.
- Regulatory Compliance: Adhering to industry regulations ensures safety and environmental responsibility.
- Future Trends: Innovations in lubrication technology will continue to evolve, providing better options for performance enhancement.
Future Trends in Hydraulic Grease Technology
Looking ahead, advancements in hydraulic grease technology will likely focus on several key areas:
- Biodegradable Options: As sustainability becomes more critical, the market may expand for eco-friendly hydraulic greases that reduce environmental impact.
- Performance Enhancements: New formulations may improve the ability of greases to withstand extreme temperatures, resulting in better performance in harsh conditions.
- Smart Lubrication Systems: Integration of technology will allow for real-time monitoring of grease levels and conditions, leading to timely maintenance actions.
- Nanotechnology: Future greases may incorporate nanomaterials to enhance friction reduction and provide superior protection against wear.
As the construction industry evolves, staying informed about these trends is crucial. Understanding the nuances of hydraulic hammer grease can help professionals make educated choices that enhance operational efficiency and lifespan of machinery.